供应商管理要求培训资料.ppt
《供应商管理要求培训资料.ppt》由会员分享,可在线阅读,更多相关《供应商管理要求培训资料.ppt(52页珍藏版)》请在三一办公上搜索。
1、供应商管理要求培训,CV质量保证部 程阳生,2007年11月14日,目录,日程安排,目录,1、供应商质量管理模式介绍 新产品质量管理 量产阶段质量管理 2、供应商评价 供应商选择评价 供应商业绩评价 3、品质保证体系工程 产品监查 4、纳入不良和A区不良管理 纳入不良管理 A区不良管理,一)整车开发过程质量保证程序和要求 1、质量策划 2、新车型节点管理 3、整车品质监查和对策确认 4、初期流动管理活动 二)零部件新品开发质量保证程序和要求 1、供应商QCDD评价 2、质量保证模式(ANPQP)推进 3、供应商节点风险评估 4、实物质量确认 5、零部件质量信息处置 6、生产件批准,(一)新产品
2、质量管理,一、供应商质量管理模式介绍,目前东风商用车新车型开发和新车型更新换代的速度明显加快,新车型在销售中的比重逐年攀升。如何做好新车型的质量管理工作,保证新车型的产品质量,成为公司质量保证部门的重要工作之一。基于行业、日产公司最新质量管理方法和公司目前的新车型质量保证现状,确定了东风商用车公司新产品质量管理模式,制定和并严格执行商用车新车型质量控制管理办法和供应商新产品质量控制管理办法-东风有商司发200793号和94号。,一)整车开发过程质量保证程序和要求,一、供应商质量管理模式介绍,(一)新产品质量管理,适用范围:商用车新车型从项目初始策划阶段、试装定型(S-LOT)、上线试装(PT1
3、、PT2)直至 SOP 和进入满负荷生产阶段的全过程质量控制和管理。1、战略商品:东风有限中长期商品发展战略项目,即A类商品。2、适应性改进商品:平台品种丰富拓展的商品,即B类商品,细分为三类:B1类商品:匹配的总成或系统需要性能/可靠性验证且需要重新公告(有新零部件设计且需要进行供应商选择,生产准备周期30天以上)的商品。,一)整车开发过程质量保证程序和要求,一、供应商质量管理模式介绍,附件1,(一)新产品质量管理,B2类商品:已有技术储备,匹配的总成或系统需要性能/可靠性验证或不需要验证但需要重新公告(有新增零部件且需要进行供应商选择,生产准备周期30天以上)的商品。B3类商品:已有技术储
4、备,匹配的总成或系统无需性能/可靠性验证,且产品无需公告(有新增零部件设计,但无需变更供应商,生产准备周期15天以内)的商品。,一、供应商质量管理模式介绍,一)整车开发过程质量保证程序和要求,(一)新产品质量管理,1、质量策划 在组织与策划、设计完成阶段,公司各部门重点做好策划和计划工作。商用车技术中心依据公司新车型项目计划,制定并发布产品文件。制造技术部编制和发布项目开发主日程计划、生产准备工作计划,确定并组织推进新产品零部件的生产准备工作。质量保证部制定新车型质量方针目标,编制质量保证计划,确定节点品质确认内容、品质目标和供应商零部件质量目标、整车评审。,一、供应商质量管理模式介绍,一)整
5、车开发过程质量保证程序和要求,(一)新产品质量管理,目前商用车公司新品开发导入雷诺.日产的A.N.P.Q.P.联合新产品品质程序,开发过程分组织与策划、设计完成、工装模具正规化、工艺正规化、量产后5个段,每个阶段都设定了节点目标。2、新车型节点管理 新产品开发工作实行项目节点管理,新品开发过程每个节点必须达到节点管理品质目标才能往下工序移行,确保新产品品质满足质量目标。新产品开发设立以下管理节点:S-LOTPT1PT2SOP出货。,一、供应商质量管理模式介绍,一)整车开发过程质量保证程序和要求,(一)新产品质量管理,公司新车型项目实行分级管理,对于B类项目视车型变化的具体内容可将往下工序判断会
6、议、SOP量产移行判断和出货判断合并召开,对节点管理项目可进行视同管理或删减。2.1 节点移行 在车辆试制(装)阶段对车辆、主要总成进行品质确认和各节点管理项目评价确认后,由CVE组织召开往下序移行判断会议(S-LOTPT1移行、PT1PT2移行),确认品质目标、节点管理项目达成状况,判断可否往下移行。在车辆PT2节点管理项目评价确认后,由公司质量保证责任者组织进行量产移行判断(PT2SOP)、出货判断(SOP出货),确认品质目标、节点管理项目达成状况,判断是否具备量产和正式销售条件。,一、供应商质量管理模式介绍,一)整车开发过程质量保证程序和要求,(一)新产品质量管理,一、供应商质量管理模式
7、介绍,一)整车开发过程质量保证程序和要求,2.2 新车型节点管理项目 为保证各节点的开发品质,从四个方面确定新车型节点管理项目,并根据质量方针目标确定节点管理各阶段要达成的目标(S-LOTPT1PT2SOP出货)。车辆品质要求(1)法规必要条件:符合法规的必要条件(3C、环保、其它新法规)(2)目录公告必要条件:符合车辆公告参数要求(3)车辆目标性能必要条件:设定和符合车辆性能目标(4)车辆可靠性:符合可靠性基准和设定目标(5)车辆CS-VES评价结果要满足OK-VES目标值:量产判断、出货判断 V1+V2 符合设定目标,(一)新产品质量管理,一、供应商质量管理模式介绍,一)整车开发过程质量保
8、证程序和要求,2.2 新车型节点管理项目 部品品质(1)部品性能:设定性能项目,确认结果必须为100%OK(2)部品品质:必须保证初始零部件品质(3)油脂材料性能:符合国家、行业、企业标准(4)新总成(含涂装)品质:符合规格要求,(一)新产品质量管理,一、供应商质量管理模式介绍,一)整车开发过程质量保证程序和要求,2.2 新车型节点管理项目 制造品质(1)生产准备:零部件生产准备完成率达成预定目标,过程保证能力达标。(2)工厂制造、装配品质目标达成 a.新总成品质:符合预定VES目标值 b.下线车辆品质:符合预定VES目标值 c.总成性能可靠性品质:要符合规格,(一)新产品质量管理,一、供应商
9、质量管理模式介绍,一)整车开发过程质量保证程序和要求,2.2 新车型节点管理项目 防止再发(1)重要不良再发防止达成预定目标值(2)PCS对策解决率达成预定目标值(3)保安防灾对策解决率达成预定目标值(4)VES指摘不良对策解决率达成预定目标值,(一)新产品质量管理,一、供应商质量管理模式介绍,一)整车开发过程质量保证程序和要求,3、整车品质监查确认在新车型项目开发各阶段,质量保证部等部门对试(装)车辆和主要总成进行整车品质监查(整车质量评审),进行CS-VES评价和保安防灾评价,并进行PSQC和可靠性试验。整车品质监查发现的质量问题,质量保证部组织相关单位进行现车问题确认、明确责任单位,组织
10、制定对策并进行对策确认,确保质量问题得到有效的整改和关闭,对V1和V2倾向性项目必须在样车时就得到纠正解决。对于责任单位采取的纠正/预防对策及样车的整改效果,质量保证部组织进行逐一确认。,(一)新产品质量管理,一、供应商质量管理模式介绍,一)整车开发过程质量保证程序和要求,4、初期流动管理活动 在SOP后量产阶段,为使在早期未能觉察的或未得到彻底解决的质量问题得到有效的解决,开展初期流动管理活动。质量保证部负责初期流动管理活动的组织工作,负责该阶段质量问题的质量分析活动和指责问题的责任判定工作。对于SOP后暴露或早期未得到彻底解决的产品设计问题,由商用车技术中心负责原因分析和对策关闭工作。,(
11、一)新产品质量管理,一、供应商质量管理模式介绍,一)整车开发过程质量保证程序和要求,5、特别工作组(Task Force)活动 为了对新品投放市场初期的质量信息早期收集确认、早期根本对策、早期市场处置,开展特别工作组(Task Force)活动。质量保证部负责特别工作组活动计划的策划、组织、推进实施。、SOP后适应性改进商品的管理 对于适应性改进商品(B类项目)视车型变化的具体内容可对初期流动管理、特别工作组活动进行简化或删减。,(一)新产品质量管理,一、供应商质量管理模式介绍,二)新产品零部件供应商质量保证,1、新产品供应商质量评价(QCDD)供应商的质量管理水平的高低,直接影响着新产品零部
12、件的开发质量,客观公正的对已经或者可能成为东风商用车零部件供应商进行QCDD评价。评价人员根据要因系和结果系的评价等级综合判断供应商的综合等级,按评价的综合等级情况作为新品供应商选择依据。2、联合新产品质量程序(ANPQP)推进 供应商新产品零部件开发过程严格执行联合新产品质量程序(ANPQP),供应商要清楚所承担零部件的质量目标,确保产品实物质量、过程质量控制和生产准备进度符合规定要求。供应商在组织与策划、设计完成、工装模具正规化、工艺正规化、SOP后五个阶段按照商用车公司要求将推行ANPQP过程中制定的相关ANPQP文件提交到DFL,经DFL评审、审批后按文件内容实施。各阶段提交文件见AN
13、PQP提交文件清单。,(一)新产品质量管理,ANPQP提交文件清单,一、供应商质量管理模式介绍,一、供应商质量管理模式介绍,一、供应商质量管理模式介绍,二)新产品零部件供应商质量保证,制造技术部负责组织供应商ANPQP推进工作,负责向供应商提出具体要求,明确ANPQP文件提交日程计划、负责接收供应商提交的ANPQP文档、负责在DFL内部传递、负责将审批后的文档返回供应商。为便于新产品零部件的分类管理,新产品零部件根据产品重要度和供应商质量管理水平分为高风险件和低风险件。新产品零部件必须经过DFL的生产件批准(PPAP),才能进入量产初期阶段正式批量向主机厂供货。,(一)新产品质量管理,一、供应
14、商质量管理模式介绍,二)新产品零部件供应商质量保证,3、供应商节点开发风险评估 在新产品零部件开发阶段,制造技术部等相关部门随时对供应商开发情况进行监查和跟踪推进。为掌控和强化零部件开发过程管理,DFL在设计完成、工装模具正规化、工艺正规化三个阶段结束前对供应商进行监查和开发风险评估,对新产品零部件ANPQP执行情况、生产准备进度和开发进展情况进行评审和确认,消除零件开发风险,推进问题整改,确保零部件开发预期的SOP时间和QCD目标实现。供应商的监查及风险评估由制造技术部负责组织,质量保证部、商用车技术中心、SCM部等部门参加。根据供应商及零部件的风险程度,由组织部门确定监查频次及监查内容。对
15、供应商的监查及风险评估应出具评估报告,要求供应商制定纠正预防措施,限期整改,下一轮监查时要跟踪验证。根据评估结果可采取以下对策:通过、预警(限期整改)、警告(准备启动B点)、切换供应商等。供应商对评估问题认真分析原因,并于一周内将措施计划报DFL,对策措施要落实到技术文件中。,(一)新产品质量管理,一、供应商质量管理模式介绍,二)新产品零部件供应商质量保证,4、实物质量确认 质量确认方式综合各方信息可采取供应商自检、入库检验和供应商现场确认三种方式。各节点试制(装)件必须(重要/关键项100%合格,总项次合格率92%,单品性能试验合格)。4.1、生产样品检验卡审批制造技术部、零部件采购部负责组
16、织供应商生产样品检验卡的提交、会签和审批工作。为明确和统一新产品零部件质量检验项目和技术要求,新产品零部件供应商在接到产品图纸、产品数模和相关技术标准后,及时将产品要求进行细化,20天内按照DFL要求填写生产样品检验卡,并报商用车技术中心、制造技术部和质量保证部进行会签和审批。制造技术部负责组织供应商生产样品检验卡的提交、会签和审批工作。新产品零件在设计更改或技术要求发生更改时,生产样品检验卡必须重新编写和审批。,(一)新产品质量管理,一、供应商质量管理模式介绍,二)新产品零部件供应商质量保证,4.2、供应商自检 供应商严格控制新产品零部件产品实物质量,保证合格产品装车,并做好检验工作。供应商
17、对新产品零部件试制样件和DFL新车型S-LOT、PT1和PT2各节点试装的新产品零件,必须按照经审批的生产样品检验卡中规定的检验项目和技术要求,对试装零部件进行全尺寸(包括尺寸、材料、外观和工程试验)检验,并将检验结果填写经审批的生产样品检验卡(附简图,检验项目要与简图上编号一一对应)。以上检验结果一式二份,一份随零件发往装配厂,必要时按报告内容进行复检和质量追溯;另一份在DFL要求时,发往质量保证部(S-LOT阶段发送到商用车技术中心试制部)。4.3、入库检验 SCM部在新车型S-LOT、PT1和PT2各节点试装前下发生产计划时,对装车用新产品零部件要求供应商将自检结果随零件发往装配厂。装配
18、厂及相关单位质量部门负责新产品零件的入库检查,对不合格零部件及时进行处置。并做好供应商自检记录的管理,必要时按报告内容进行复检和质量追溯。供应商对不合格零部件及时现场处置,并做好原因分析和质量改善活动。,(一)、新产品质量管理,一、供应商质量管理模式介绍,二)新产品零部件供应商质量保证,4.4、供应商现场质量确认 根据零部件的重要和风险程度以及供应商的质量水平,质量保证部相关部门在开发过程中组织对试装零部件到供应商现场进行检验和试验,对风险度低的零部件可对供应商提交的自检报告进行审核确认。对供应商现场质量确认时发现的不合格质量保证部将纳入质量考核。5、零部件质量信息处置 在新车型开发过程中,在
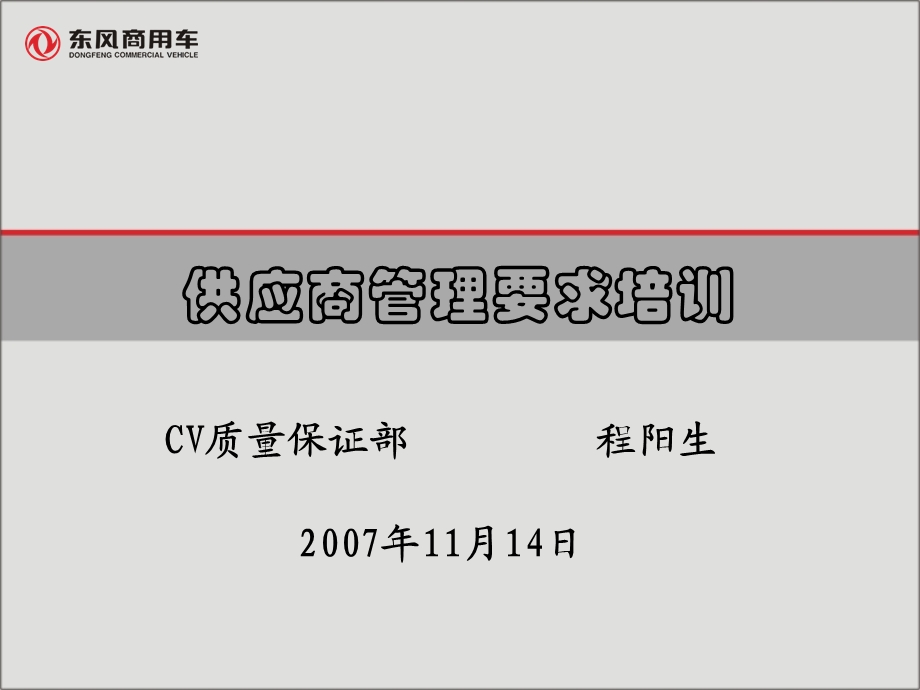


- 配套讲稿:
如PPT文件的首页显示word图标,表示该PPT已包含配套word讲稿。双击word图标可打开word文档。
- 特殊限制:
部分文档作品中含有的国旗、国徽等图片,仅作为作品整体效果示例展示,禁止商用。设计者仅对作品中独创性部分享有著作权。
- 关 键 词:
- 供应商 管理 要求 培训资料

链接地址:https://www.31ppt.com/p-6549133.html