机械加工质量分析及控制.ppt
《机械加工质量分析及控制.ppt》由会员分享,可在线阅读,更多相关《机械加工质量分析及控制.ppt(107页珍藏版)》请在三一办公上搜索。
1、第3章 机械加工质量分析及控制,第一节 概述第二节 影响加工精度的主要因素及其控制第三节 加工误差的综合分析第四节 影响表面质量的因素及其控制第五节 机械加工中振动的基本知识,第一节 概 述,零件的加工质量是保证机械产品工作性能和产品寿命的基础。,衡量进行加工质量的指标有两方面,加工精度表面质量,本章的任务是讨论零件的机械加工精度问题。,一、加工精度和表面质量的概念,在机械加工过程中,由于各种因素的影响,使刀具和工件间的正确位置发生偏移,因而加工出来的零件不可能与理想的要求完全符合,两者的符合程度可用机械加工精度和加工误差来表示。,是指零件加工后的实际几何参数(尺寸、形状和位置)与理想几何参数
2、的符合程度。,1、机械加工精度:,2、加工误差:,是指零件加工后的实际几何参数(尺寸、形状和位置)与理想几何参数的偏离程度。加工精度越高,则加工误差越小,反之越大。,从保证产品的使用性能分析,没有必要把每个零件都加工得绝对准确,可以允许有定的加工误差,只要加工误差不超过图样规定的偏差,即为合格品。,加工精度的高低是以国家有关公差标准来表示的。保证和提高加工精度实际上就是限制和降低加工误差。,3、表面质量(一)加工表面几何特征 加工表面的几何特征,主要由表面粗糙度和表面波度两部分组成(见图3-1)。(二)加工表面层物理力学性能,图3-1表面粗糙度和波度,(1)试切法,应用:单件小批生产中。,方法
3、:对工件进行试切测量调整再试切,直到达到要求的精度为止。,二、加工精度的获得方法,1)测量误差。由量具本身精度度、测量方法及使用条件引起。2)进给机构的位移误差。在微量调整刀具的位置、低速微量进给中,常常出现进给机构的“爬行”现象,其结果使刀具的实际位移与刻度盘上的数值不一致、造成加工误差。3)试切时与正式切削时切削层厚度不同的影响。精加工时,切削刃只起挤压作用而不起切削作用,但正式切削时的深度较大工件。,这时,引起调整误差的因素有:,(2)调整法,影响调整精度的因素有:,1)上述影响试切法调整精度的因素,因为采用调整法对工艺系统进行调整时,也要以试切为依据。2)用定程机构调整时,调整精度取决
4、于行程挡块、靠模及凸轮等机构的制造精度和刚度;,3)用样件或样板调整时,调整精度取决于祥件或样板的制造、安装和对刀精度;4)工艺系统初调好以后,般要试切几个工件,并以其平均尺寸作为判断调整是否准确的依据。由于试切加工的工件数(称为抽样件数)不可能太多,不能完全反映整批工件切削过程中的各种随机误差,故试切加工几个工件的平均尺寸与总体尺寸不能完全符合,也造成加工误差。,三、加工表面质量对零件使用性能的影响,1.表面质量对零件耐磨性的影响,(1)表面粗糙度对零件耐磨性的影响 一对刚加工好的摩擦副的两个接触表面之间,最初阶段只是在表面粗糙度的峰部接触,实际接触面积远小于理论接触面积,在相互接触的峰部,
5、有非常大的单位压力,使实际接触面积处产生塑性变形、弹性变形和峰部之间的剪切破坏,引起严重磨损。,零件磨损的特点:零件磨损一般可分为三个阶段,图中、和三个区域分别表示了这三个阶段。,:磨损快、时间较短。,:随着表面粗糙度峰部不断被碾平和被剪切,实际接触面积不断加大,单位压力也逐渐减小,摩擦副即进入正常磨损阶段。正常磨损阶段经历的时间较长。,:随着表面粗糙度的峰部不断被碾平和被剪切,接触面积越大,零件间的金属分子亲和力增大,表面间机械咬合作用增大,磨损急剧增加。区是剧烈磨损区,此时摩擦副不能正常工作。,磨损量,工作时间,初期磨损阶段,正常磨损阶段,剧烈磨损阶段,表面粗糙度对零件表面磨损的影响很大。
6、一般说来,表面粗糙度值越小,其耐磨性越好。但表面粗糙度值太小,润滑油不易储存,接触面之间容易发生分子粘接,磨损反而增加。因此,接触面的表面粗糙度有一个最佳值一般由试验确定。,平均磨损量,%,表面粗糙度,发动机活塞销最合适的表面粗糙度值,(2)表面冷作硬化对零件耐磨性的影响,加工表面的冷作硬化,使摩擦副表面层金属的显微硬度提高,减少了摩擦副接触处的弹性和塑性变形,故一般可使耐磨性提高。,但也不是冷作硬化程度越高耐磨性也越高,这是因为过分的冷作硬化将引起金属组织过度疏松,甚至出现裂纹和表层金属的剥落,使耐磨性下降。,磨损量,HB,320,340,360,380,400,420,440,50,60,
7、70,80,90,2.表面质量对零件疲劳强度的影响 金属受交变载荷作用后产生的疲劳破坏往往发生在零件表面或表面冷硬层下面,因此零件的表面质量对疲劳强度影响较大。(1)表面粗糙度对零件疲劳强度的影响 在交变载荷作用下,表面粗糙度的凹谷部位容易引起应力集中,产生疲劳裂纹。表面粗糙度值越大,表面的裂纹越深,纹底半径越小,抗疲劳破坏的能力越差。零件上易产生应力集中的沟槽、圆角等处的表面粗糙度,对疲劳强度的影响更大。,(2)残余应力对零件疲劳强度的影响 残余应力对疲劳强度强度的影响较大。表面残余拉应力将使疲劳裂纹扩大,加速疲劳破坏;而表面残余压应力能够阻止疲劳裂纹的扩展,延缓疲劳破坏的发生,有利于提高疲
8、劳强度。(3)冷作硬化对零件疲劳强度的影响 表面冷作硬化一般伴有残余压应力的产生,可以防止裂纹产生并阻止已有裂纹的扩展,对提高疲劳强度有利。但表面冷作硬化过高时,可能会产生较大的脆性裂纹,从而降低疲劳强度。,3.表面质量对耐腐蚀性能的影响,(1)表面粗糙度对零件耐蚀性的影响,大气里气体、液体与金属工件接触,会在金属表面凝聚而使金属腐蚀。表面粗糙度越大,接触面越大,腐蚀物质越易沉积于凹坑中,耐蚀性越差。,(2)表面层金属力学物理性能对零件耐蚀性的影响 当零件表面有残余压应力时,有利于阻止表面裂纹的进一步扩大,耐蚀性提高;当零件表面有残余拉应力时,则会使表面裂纹的进一步扩大,耐蚀性变差。,4.表面
9、质量对零件配合质量的影响,(1)间隙配合,对于间隙配合,工作表面越粗糙,磨损越大,使配合间隙很快增大,从而改变原有的配合性质,降低配合精度。对于液压、气动元件,还会造成泄露量增大;,(2)过盈配合,对于过盈配合,由于在轴压入孔时,表面粗糙度的部分凸峰被挤平,而使过盈量减小,降低了连接强度,影响配合的可靠性。,因此,具有配合精度要求的表面,需具有较小的表面粗糙度。,三、影响表面质量的工艺因素,1、表面粗糙度,在切削加工中刀具的几何形状、切削用量、切削液、振动等工艺因素,都会影响表面粗糙度。,(1)几何因素,在切削过程中,刀具的刃口圆角及后刀面的挤压与摩擦使金属材料发生塑性变形而使理论残留面积挤歪
10、或沟纹加深,因而增大了表面粗糙度。,实际轮廓,理论轮廓,(2)物理因素 切削加工后表面粗糙度的实际轮廓之所以与纯几何因素所形成的理论轮廓有很大的差异,主要是由于切削过程中塑性变形的影响。,在切削过程中出现刀瘤(积屑瘤),积屑瘤形成后并不是稳定不变的,而是不断地形成、长大,然后粘附在切屑上被带走或留在工件上。由于积屑瘤有时会伸出切削刃之外,其轮廓也很不规则,因而使加工表面上出现深浅和宽窄都不断变化的刀痕,大大恶化了表面粗糙度。,积屑瘤是切削过程中切屑底层与前刀面冷焊的结果。,加工塑性材料时,切削速度为中、低速,易产生积屑瘤。,在切削过程出现鳞刺 鳞刺是已加工表面上出现的鳞片状毛刺般的缺陷。切削过
11、程中出现鳞刺是由于切屑在前刀面上的摩擦和冷焊作用造成周期性地停留,代替刀具推挤切削层,造成切削层和工件之间出现撕裂现象。,I.抹拭,II.沉积,III.导裂,IV.刮成,鳞刺的形成过程,2.表面层的冷作硬化,(1)加工硬化(或冷作硬化)定义 机械加工时,工件表面层金属受到切削力的作用产生强烈的塑性变形,使晶格扭曲,晶粒间产生剪切滑移,晶粒被拉长、纤维化甚至碎化,从而使表面层的强度和硬度增加,这种现象称为加工硬化,又称冷作硬化和强化。,但在加工过程中所产生的切削热又将使冷作硬化弱化,故硬化程度取决于强化和弱化的综合。,(2)衡量表面层加工硬化的指标表面层的显微硬度HR;硬化层深度h;硬化程度N,
12、HR0:工件原表面层的显微硬度。,(1)表面残余应力的产生机理 当切削及磨削过程中加工表面相对于基体材料发生形状、体积变化或金相组织变化时,在加工后表面层中将残留有应力,应力大小随深度而变化,其最外层的应力和表面层与基体材料交界处(以下简称里层)的应力符号相反,并相互平衡。表面层组织发生变化时,在表面层及其与基体材料的交界处会产生互相平衡的弹性力。这种应力即为表面层的残余应力。,3.表层金属的残余应力,冷塑性变形的影响 在切削加工过程中,工件表面层受切削力的作用,会拉长表层金属的纤维,产生塑性变形,使表层金属的比容增大,导致体积膨胀;刀具后刀面与已加工表面的摩擦,会加大这种拉伸作用。但表层金属
13、体积膨胀会受到与之相连的里层金属的阻碍。故:在加工时,表层产生拉应力,里层处于弹性变形状态下。,(1)冷塑性变形的影响 当切削加工完成后,切削力已去除,里层金属趋向复原(弹性恢复),但受到已产生塑性变形的表面层限制,回复不到原状,因而在表面层产生残余压应力,里层则为拉应力与之相平衡。,(2)热塑性变形的影响 表面层在切削热的作用下产生热膨胀,此时基体温度较低,因此表面热膨胀受到基体的限制而产生热压缩应力。当表面层的温度超过材料的弹性变形的温度范围时,就会产生热塑性变形(在压力作用下材料相对缩短)。当切削过程结束,温度下降至与基体温度一致时,因为表面层已产生热塑性变形,但受到基体的限制产生拉应力
14、,里层则为残余压应力。,距表层深度,4.金相组织变化的影响 切削时产生的高温会引起表面层的相变。由于不同的金相组织有不同的比重,表面层金相组织变化的结果造成了体积的变化。表面层体积膨胀时,因为受到基体的限制,产生压应力;反之表面层体积缩小,则产生拉应力。各种金相组织中,马氏体比重最小,奥氏体比重最大。,磨削淬火钢时若表面产生回火现象,马氏体转变成索氏体或屈氏体(这两者组织均为扩散程度很高的珠光体),因体积缩小,表面层产生残余拉应力,里层产生残余压应力。若表面层产生二次淬火现象,则表面层产生二次淬火马氏体,其体积比里层的回火组织大,因而表层产生压应力,里层产生拉应力。,四、提高零件疲劳强度的加工
15、方法,(1)喷丸强化 喷丸强化是利用大量快速运动的珠丸打击被加工工件表面,使工件表面产生冷硬层和残余压应力,可显著提高零件的疲劳强度。珠丸可以是铸铁的,也可以是切成小段的钢丝(使用一段时间后,自然变成球状)。喷丸强化主要用于强化形状复杂或不宜用其它方法强化的工件,如板弹簧、螺旋弹簧、连杆、齿轮、焊缝等。经喷丸加工后的表面,硬化层深度可达0.7mm,零件表面粗糙度值可由52.5m 减小到0.630.32m(Ra),可几倍甚至几十倍地提高零件的使用寿命。,滚压加工原理,(2)滚压加工 滚压加工是利用经过淬火和精细研磨过的滚轮或滚珠,在常温状态下对金属表面进行挤压,使受压点产生弹性和塑性变形,表层的
16、凸起部分向下压,凹下部分向上挤,逐渐将前工序留下的波峰压平,降低了表面粗糙度;同时它还能使工件表面产生硬化层和残余压应力。因此提高了零件的承载能力和疲劳强度。,单滚柱滚压,滚压加工可以加工外圆、孔、平面及成型表面,通常在普通车床、转塔车床或自动车床上进行。,五、机械加工过程的中振动,机械加工过程中产生的振动,是一种十分有害的现象。它将导致:,刀具与工件产生位移而使加工表面产生波纹;,加剧刀具磨损,甚至崩刃;,机床联接特性受到破坏;,危害人的健康;,(一)、机械加工精度 1.机械加工精度:零件加工以后的实际几何参数与理想几何参数的接近程度。(宏观几何特征),六、机械加工精度及其控制,机械加工质量
17、,机械加工精度,加工表面质量,尺寸精度、形状精度、位置精度,理想零件尺 寸:零件尺寸的公差带中心。表面形状:绝对准确的圆柱面、圆锥面、平面等。表面位置:绝对的平行、垂直、同轴等。,2.加工误差 所谓加工误差是指实际零件与理想零件在几何参数上的偏离程度。由此可见:加工精度和加工误差这两个概念是从两个观点来评定零件几何参数这个同一事物的。,目前,还没有加工手段可以将零件的几何参数制作成百分百的准确存在误差。只要能保证零件在机器中的功能,把零件的加工精度保持在一定的范围之内是完全允许的合理规定公差。,尺寸精度的高低用尺寸公差来体现:国家标准分为20级,IT1、IT2、IT3、IT4、IT5、IT6、
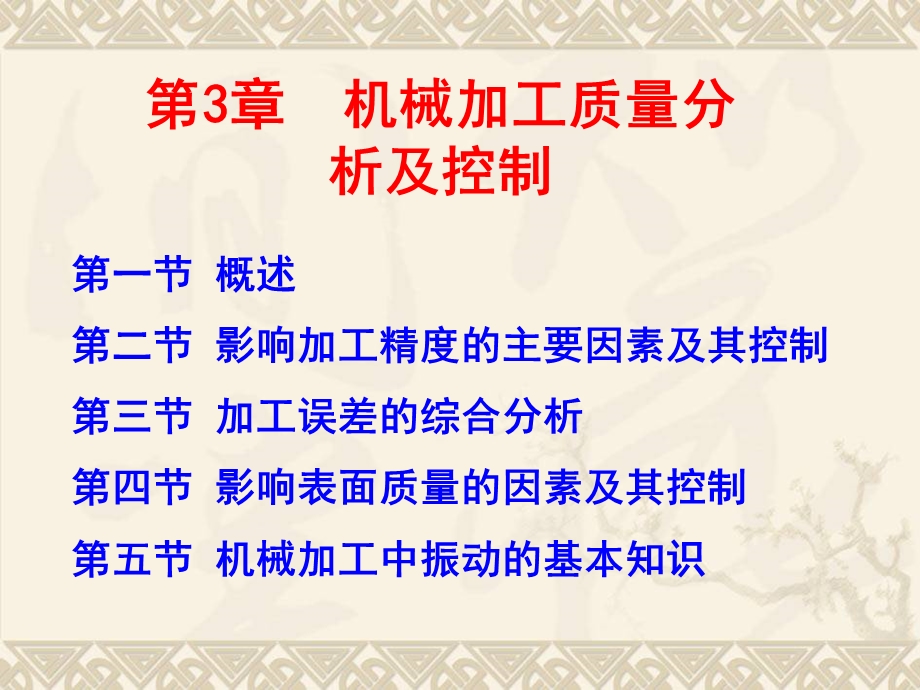

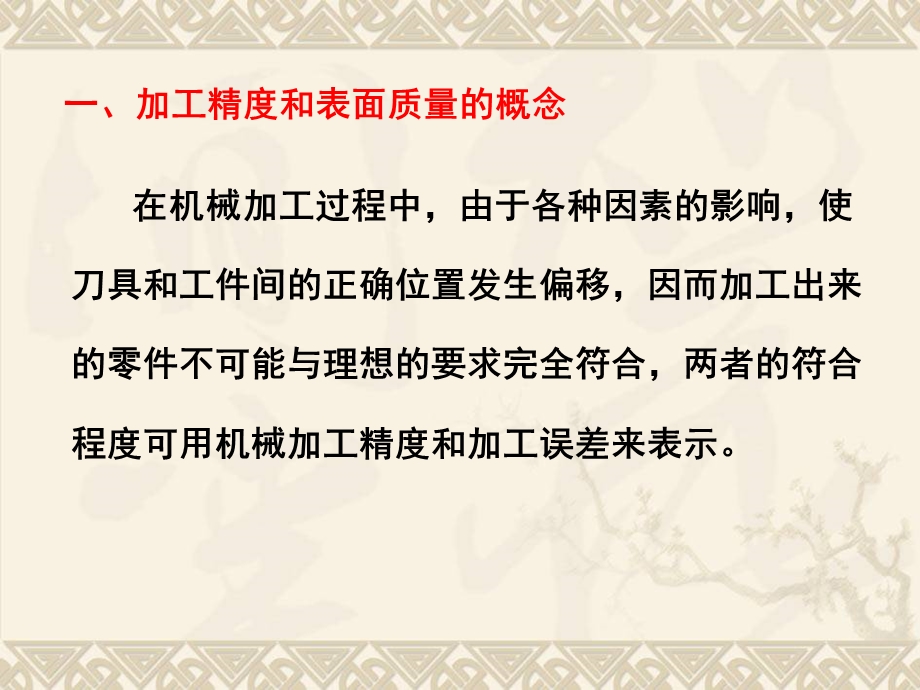
- 配套讲稿:
如PPT文件的首页显示word图标,表示该PPT已包含配套word讲稿。双击word图标可打开word文档。
- 特殊限制:
部分文档作品中含有的国旗、国徽等图片,仅作为作品整体效果示例展示,禁止商用。设计者仅对作品中独创性部分享有著作权。
- 关 键 词:
- 机械 加工 质量 分析 控制

链接地址:https://www.31ppt.com/p-5756734.html