机械制造技术课程设计说明书 制定C6132车床I轴加工工艺及钻Φ8孔夹具设计【全套图纸】.doc
《机械制造技术课程设计说明书 制定C6132车床I轴加工工艺及钻Φ8孔夹具设计【全套图纸】.doc》由会员分享,可在线阅读,更多相关《机械制造技术课程设计说明书 制定C6132车床I轴加工工艺及钻Φ8孔夹具设计【全套图纸】.doc(38页珍藏版)》请在三一办公上搜索。
1、哈尔滨理工大学课程设计说明书不要删除行尾的分节符,此行不会被打印机械制造技术课程设计说明书设计题目:制定C6132机床轴的加工工艺,设 计钻孔的钻床夹具 专 业: 机电一体化技术 班 级: 2011级2班 学 号: 1130320203 姓 名: 指导教师: 机械工程系 2013年11月15日 目录一 课题介绍.41.1 课题4二 车床I轴的工作条件与技术要求42.1 支承轴颈的技术要求42.2 空套齿轮轴颈的技术要求5三 I轴的选材与原因5四 材料的热处理.6五 制定加工工艺路线.65.1 I轴加工工艺过程分析6 5.2 工艺路线的拟定.7 5.3 加工余量的确定.10六 轴类零件的检验.1
2、0 6.1 加工中的检验.10 6.2 加工后的检验.10七 确定切削用量及基本工时.11 7.1 粗车40右端面.11 7.2 钻24孔.13 7.3 粗车M36 左端面.14 7.4 半精车40右端面15 7.5 半精车M36左端面.167.6 精车40右端面177.7 精车M36左端面18 7.8 粗车40外圆19 7.9半精车40外圆21 7.10 半精车40外圆.23 7.11 半精车40外圆.24 7.12 倒角.26 7.13 倒角.26 7.14 车过渡圆.26 7.15 磨削外圆.29八 钻8孔的钻床夹具计.31 8.1 定位基准的选择.31 8.2 切削力及夹紧力计算32
3、8.3 定位误差分析32总结.34参考文献.35千万不要删除行尾的分节符,此行不会被打印。在目录上点右键“更新域”,然后“更新整个目录”。打印前,不要忘记把上面“Abstract”这一行后加一空行 一、课题介绍1.1课题车床I轴是车床的主要零件,它的头端装有夹具、工件或刀具,工作时要承受扭曲和弯矩,所以要求有足够的刚性、耐磨性和抗振性,并要求很高的回转精度。所以主轴的加工质量对机床的工作精度和使用寿命有很大的影响。全套图纸,加153893706二、车床I轴的工作条件与技术要求a.承受摩擦与磨损 机床I轴的某些部位承受着不同程度的摩擦,特别是轴颈部位,因为轴颈与某些轴承配合时,摩擦较大所以此部位
4、应具有较高的硬度仪增强耐磨性。但是某些部位的轴颈与滚动轴承相配合摩擦不大,所以就不需要大的硬度。b.工作中时承受载荷 机床I轴在高速运转时要承受多种载荷的作用,如弯曲、扭转、冲击等。所以要求主轴具有抵抗各种载荷的能力。当主轴载荷较大、转速又高时,主轴还承受着很高的变交应力。因此要求主轴具有较高的疲劳强度和综合力学性能即可。2.1、支承轴颈的技术要求I轴两支承轴颈A、B的圆度允差 0.005毫米,径向跳动允差 0.005毫米,两支承轴颈的1:12锥面接触率70%,表面粗糙度Ra0.4um。支承轴颈直径按IT5-7级精度制造。I轴外圆的圆度要求,对于一般精度的机床,其允差通常不超过尺寸公差的50,
5、对于提高精度的机床,则不超过25%,对于高精度的机床,则应在 510之间。2.2 空套齿轮轴颈的技术要求 空套齿轮的轴颈对支承轴颈A、B的径向跳动允差为 0.015毫米。从上述分析可以看出,I轴的主要加工表面是两个支承轴颈、前端其端面、以及装齿轮的各个轴颈等。而保证支承轴颈本身的尺寸精度、几何形状精度、两个支承轴颈之间的同轴度、支承轴颈与其它表面的相互位置精度和表面粗糙度,则是主轴加工的关键。 三、I轴的选材与原因选材选用45钢即可 因为I轴承受变弯曲应力与扭转应力,但由于承受的载荷并不是很大,转速也不高,冲击作用也不大,所以具有一般的综合力学性能即可。但因为I轴大端的内锥孔和外锥孔处,因经常
6、与卡盘、顶尖有相对摩擦;花键部位与齿轮有相对滑动,所以这些部位要求较高的硬度与耐磨性。45钢的钢性虽淬透性较差,但主轴工作时最大应力分布在表面,在粗车后,轴的形状较简单,在调质淬火时一般不会开裂。因此选用合金调质钢,采用廉价、可锻性和切割加工性皆好的45钢即可。车床主轴直径较大,阶梯较多,宜选锻件毛坯。并且节约原材料和减少加工工时。 四、材料的热处理热处理技术条件为整体调质,硬度为220250HBS,内锥孔与外锥体淬火,硬度4550HRC;花键部位高频淬火,硬度4853HRC。内锥孔和外锥体用盐炉快速加热并水淬,外锥体键槽不淬硬,要注意保护。花键要用高频淬火以减少变形并达到表面淬硬的要求。由于
7、轴较长,且锥孔与外锥体对两轴劲的同轴度较高,故锥部淬火应与花键淬火分开进行,以减少淬火变形;随后用粗磨校正淬火变形,然后再进行花键的加工与淬火,其变形可用最后精磨予以消除。 五、 制定加工工艺路线拟订零件的加工路线是制定工艺规程的总体布局,主要任务是选择各表面的加工方法,及定位基准,确定加工顺序,各工序采用的机床设备和工艺装备等。5.1 I轴加工工艺过程分析主轴加工工艺过程可划分为三个加工阶段,即粗加工阶段(包括铣端面、粗车外圆等);半精加工阶段(半精车外圆,钻深孔,锥孔,钻大头端面各孔,精车外圆等);精加工阶段(包括精铣键槽,粗、精磨外圆等)。在机械加工工序中间尚需插入必要的热处理工序,这就
8、决定了主轴加工各主要表面总是循着以下顺序的进行,即粗车调质(预备热处理)半精车精车淬火-回火(最终热处理)粗磨精磨。综上所述,主轴主要表面的加工顺序安排如下:外圆表面粗加工(以顶尖孔定位)外圆表面半精加工(以顶尖孔定位)钻深孔(以半精加工过的外圆表面定位)外圆表面精加工(以锥堵顶尖孔定位)钻孔精加工(以精加工外圆面定位)。当主要表面加工顺序确定后,就要合理地插入非主要表面加工工序。对主轴来说非主要表面指的是螺孔、键槽、螺纹等。这些表面加工一般不易出现废品,所以尽量安排在后面工序进行,主要表面加工一旦出了废品,非主要表面就不需加工了,这样可以避免浪费工时。但这些表面也不能放在主要表面精加工后,以
9、防在加工非主要表面过程中损伤已精加工过的对凡是需要在淬硬表面上加工的螺孔、键槽等,都应安排在淬火前加工。非淬硬表面上螺孔、键槽等一般在外圆精车之后,精磨之前进行加工。主轴螺纹,因它与主轴支承轴颈之间有一定的同轴度要求,所以螺纹安排在以非淬火-回火为最终热处理工序之后的精加工阶段进行,这样半精加工后残余应力所引起的变形和热处理后的变形,就不会影响螺纹的加工精度。5.2、工艺路线的拟定为保证几何形状、尺寸精度、位置精度及各项技术要求,必须判定合理的工艺路线。序号工序名称工 序 内 容定位基准设 备5备 料 10锻 造磨 锻 立式精锻机15热处理正 火 回火炉20锯 头锻件两端切平 锯 床25铣端面
10、打中心孔同车量端面,钻的中心孔小端外形专用机床30荒 车粗车各段外径,均放余量为2.53mm大端外形及断面、小端中心孔卧室车床35热处理调质220240HB40车大端各部右端大外圆车刀尺寸:车端面C成40mm外圆:车端面A,倒角,切退刀槽大端外形,小端中心孔卧式车床C620B45车小端各部车小端各部外圆40外圆,D面,小端中心孔液压半自动仿形车床50钻深孔钻主轴通孔至尺寸M24X1.5,40f7外圆及小断面专用深孔钻床55热处理高频局部淬火:达图样要求高频淬火机60精车精车各外圆并车槽 端面中心孔和端面 数控车床CSK616365粗磨外圆粗磨40n6和48a11外圆两段端面中心孔和端面万能外圆
11、磨床M1433B70铣花键粗,精铣键到图样尺寸端面中心孔和端面花键铣床YB601675铣键槽铣键槽到尺寸40js6外圆及A面铣床X5280车螺纹车小端外侧螺纹配螺纹端面中心孔和端面卧式车床85磨外圆精磨各档外圆,A、B面端端面中心孔和端面万能外圆磨床M1432A90检 查按图样技术要求项目检查 工艺路线方案工艺路线的分析:工艺路线方案采用先铣面,后钻孔的思路,符合工序集中和先面后孔的原则,但在加工右边圆柱上平面和左边圆柱下平面时不便于定位和装夹,且不符合基准先行的原则;而加工方案不仅符合先面后孔的原则和基准先行原则,而且便于定位和装夹。5.3 加工余量的确定工艺路线拟定以后,应确定每道工序的加
12、工余量、工序尺寸及其公差。工序尺寸是工件加工过程中,每个工序加工应保证的尺寸,工序尺寸允许的变动范围就是工序尺寸的公差。工序尺寸的确定与加工余量有着密切的关系。零件图上的尺寸和公差就是最终的加工工序尺寸和公差。将此尺寸加上加工余量就是上一工序的工序尺寸。 六、轴类零件的检验6.1、加工中的检验 自动测量装置,作为辅助装置安装在机床上。这种检验方式能在不影响加工的情况下,根据测量结果,主动地控制机床的工作过程,如改变进给量,自动补偿刀具磨损,自动退刀、停车等,使之适应加工条件的变化,防止产生废品,故又称为主动检验。主动检验属在线检测,即在设备运行,生产不停顿的情况下,根据信号处理的基本原理,掌握
13、设备运行状况,对生产过程进行预测预报及必要调整。在线检测在机械制造中的应用越来越广。6.2、加工后的检验单件小批生产中,尺寸精度一般用外径千分尺检验;大批大量生产时,常采用光滑极限量规检验,长度大而精度高的工件可用比较仪检验。表面粗糙度可用粗糙度样板进行检验;要求较高时则用光学显微镜或轮廓仪检验。圆度误差可用千分尺测出的工件同一截面内直径的最大差值之半来确定,也可用千分表借助V形铁来测量,若条件许可,可用圆度仪检验。圆柱度误差通常用千分尺测出同一轴向剖面内最大与最小值之差的方法来确定。主轴相互位置精度检验一般以轴两端顶尖孔或工艺锥堵上的顶尖孔为定位基准,在两支承轴颈上方分别用千分表测量。 七、
14、确定切削用量及基本工时7.1 粗车40右端面(1)选择刀具选用93 偏头端面车刀,参看机械制造工艺设计简明手册车床选用C365L转塔式车床,中心高度210mm。选择车刀几何形状,前刀面形状为平面带倒棱型,前角为10,后角8,主偏角93,副偏角10,刀尖圆弧半径0.5mm,刃倾角-10。(2)确定切削用量(a)确定背吃刀量ap (即切深a )粗车的余量为4.5mm由于刀杆截面取最大吃刀深度为6mm所以一次走刀完成即ap =4.5mm。(b)确定进给量查切削用量简明手册:加工材料HT200、车刀刀杆尺寸为16*25 、工件直径100mm、切削深度a =4.5mm,则进给量为0.7-1.0。再根据C
15、365L车床及机械制造工艺设计手册表3-13 查取横向进给量取f=0.73mm/r。(c)选择磨钝标准及耐用度根据切削用量简明手册表1.9,取车刀后面最大磨损量为0.8-1.0。焊接车刀耐用度T=60mm。(d)确定切削速度V根据切削用量简明手册表1.11 当用YG6 硬质合金车刀加工HT200(182-199HBS),a =4.5mm,f=0.73mm/r,查出V =1.05m/s。由于实际情况,在车削过程使用条件的改变,根据切削用量简明手册表1.28,查得切削速度的修正系数KTv=1.0,Ktv=1.0,Kkrv=0.73,Kmv=(190/HBS)1.25=1.0,Ksv=0.85,Kk
16、v=1.0。则V = V*KTv*Ktv*Kkrv*Kmv*Ksv*Kkv=1.05*60*1.0*1.0*0.73*1.0*0.85*1.0=44m/minn =140r/min按C365L 车床转速(机械制造工艺设计手册表4.11)选择与140r/min 相近似的机床转速n=136r/min,则实际切削速度V =42.7m/min。(e)校验机床功率车削时功率P 可由切削用量简明手册表1.25 查得:在上述各条件下切削功率P =1.7-2.0,取2.0。由于实际车削过程使用条件改变,根据切削用量简明手册表1.29-2,切削功率修正系数为:Kkrpc=KkrFc=0.89,Kropc=Kro
17、Fc=1.0。则:P = P KkrpcKrop=1.87KW根据C365L车床当n =136r/min时,车床主轴允许功率PE=7.36KW。因P PE,故所选的切削用量可在C365L上加工。(f)校验机床进给机构强度车削时的进给力Ff 可由切削用量手册查表得Ff=1140N。由于实际车削过程使用条件的改变,根据切削用量简明手册查得车削过程的修正系数:Kkrf=1.17,Krof=1.0,K =0.75,则Ff =1140*1.17*1.0*0.75=1000N根据C365L车床说明书(切削用量简明手册),进给机构的进给力Fmax=4100N(横向进给)因Ff Fmax,所选的f =0.73
18、 进给量可用。综上,此工步的切削用量为:a =4.5mm,f =0.73, n =136r/min, V =42.7m/min。(3)计算基本工时:按机械制造工艺设计简明手册公式计算:L= L0+L1+L2+L3,由于车削实际端面d0=0,L1=4,L2=2,L3=5,则L=100/2+4+2+5=61mm.T= =L*i/(f*n)=611/(0.73136)=0.61min7.2 钻24孔(1)刀具选择:查机械制造工艺设计简明手册选用F18 高速钢锥柄标准花钻。(2)切削用量选择:查切削用量手册得:f=0.70-0.86mm/r,再由机械制造工艺设计简明手册C365L 车床进给量取f=0.
19、76mm/r。查切削用量简明手册取V =0.33m/s=19.8m/minn =1000V/(p D)=100019.8/3.1418=350r/min按机床选取n =322r/m,故V = p Dn/1000=3.1418322/1000=18m/min(3)计算基本工时:T=(L+L1+L2)/(fn)=(91+11+0)/(0.76322)=0.42min。其中L=91,L1=(D/2)cotKr+2=11,L2=07.3 粗车M36 左端面(1)选择刀具:与粗车F40 左端面同一把。(2)确定切削用量(a)确定背吃刀量asp粗车的余量为4.5mm由于刀杆截面取最大吃刀深度为6mm所以一
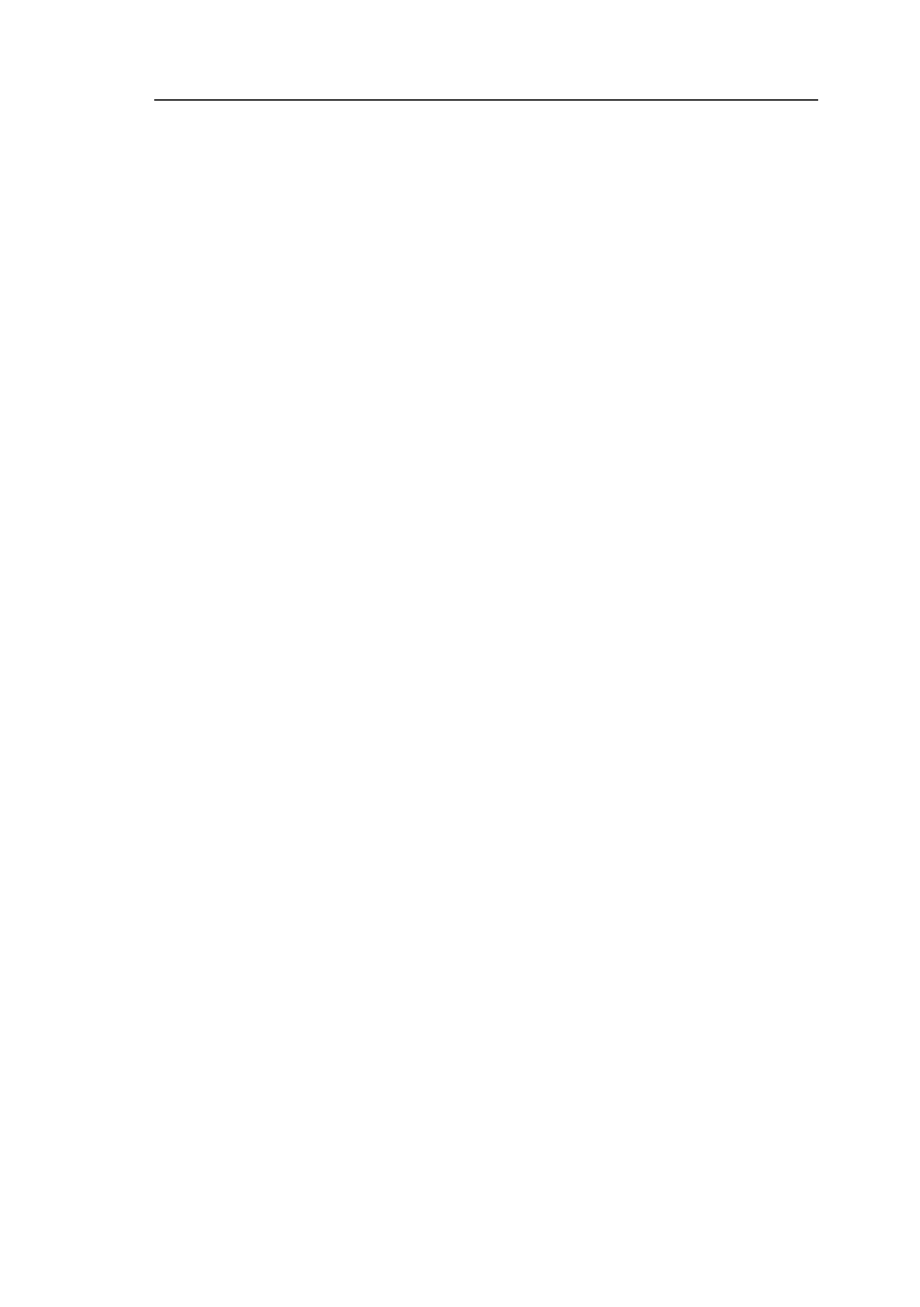
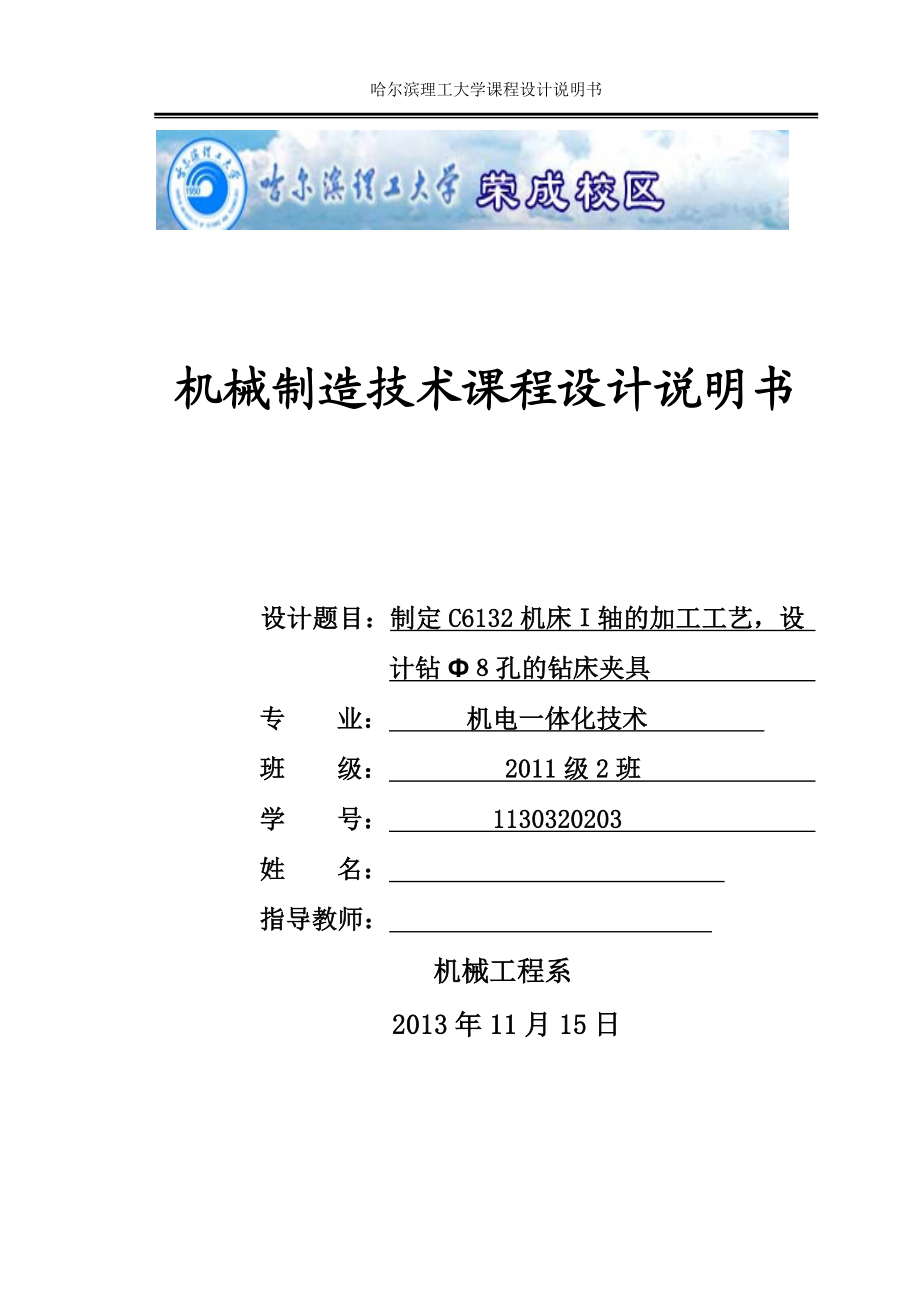
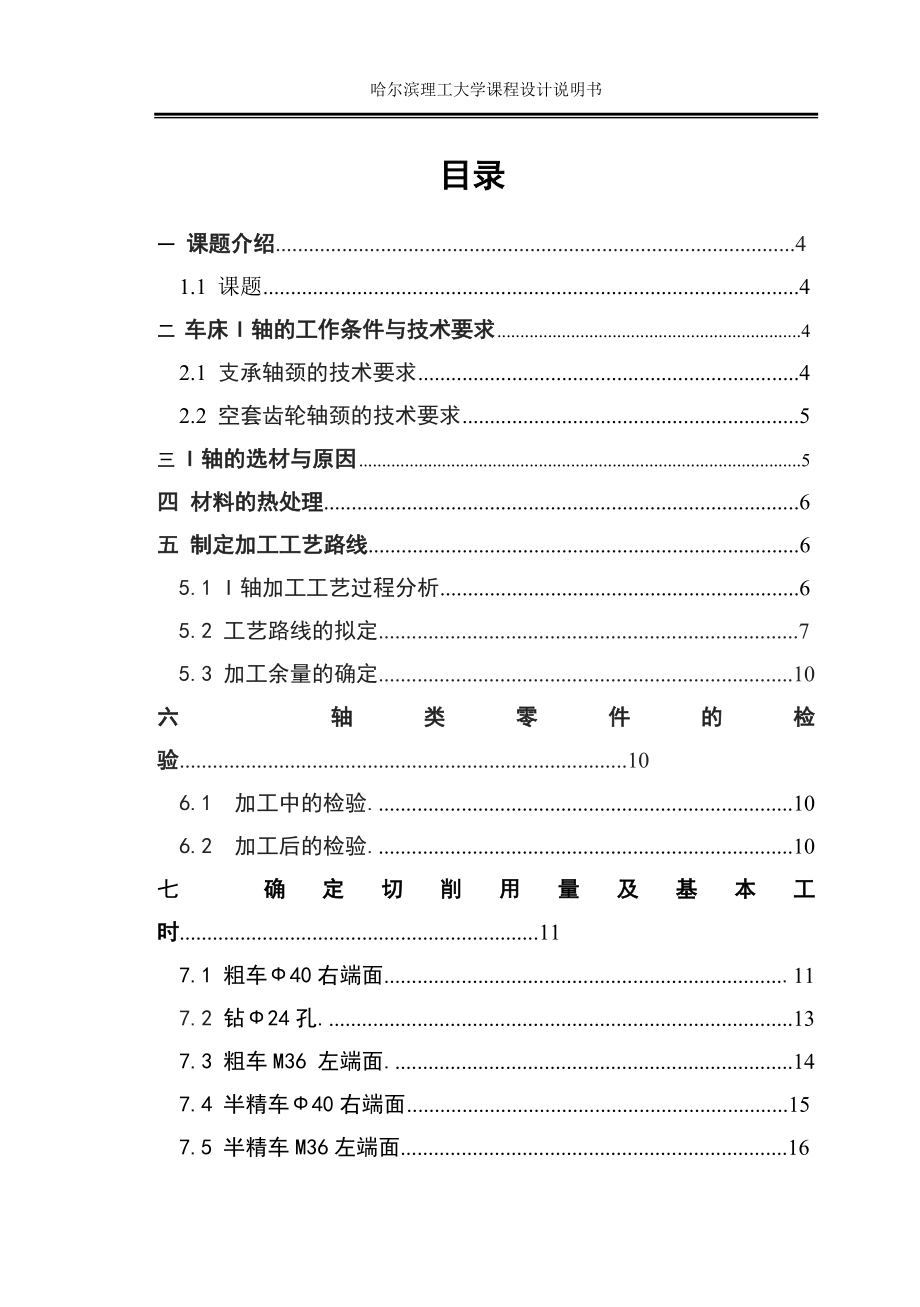
- 配套讲稿:
如PPT文件的首页显示word图标,表示该PPT已包含配套word讲稿。双击word图标可打开word文档。
- 特殊限制:
部分文档作品中含有的国旗、国徽等图片,仅作为作品整体效果示例展示,禁止商用。设计者仅对作品中独创性部分享有著作权。
- 关 键 词:
- 全套图纸 机械制造技术课程设计说明书 制定C6132车床I轴加工工艺及钻8孔夹具设计【全套图纸】 机械制造 技术 课程设计 说明书 制定 C6132 车床 加工 工艺 夹具 设计 全套 图纸

链接地址:https://www.31ppt.com/p-4841431.html