Ford福特GDT形位公差培训材料全集.ppt
《Ford福特GDT形位公差培训材料全集.ppt》由会员分享,可在线阅读,更多相关《Ford福特GDT形位公差培训材料全集.ppt(115页珍藏版)》请在三一办公上搜索。
1、GD&T for Body,GD&T for Body Engineering,2,Course content课程内容,Introduction to GD&TGD&T介绍5 Step Process5步方法,GD&T for Body Engineering,3,Introduction介绍,What is GD&T什么是GD&THow it affects Ford Motor Company它如何让影响福特汽车公司,GD&T for Body Engineering,4,What is GD&T什么是GD&T,Geometric Dimensioning and Tolerancing
2、 is a technical data base through which our Product Design and Manufacturing Organisations can talk to one another via Product Data,whether on paper or the computer graphics screen几何尺寸公差是贯穿我们产品设计和生产制造的技术数据基础,无论是通过图纸或者是计算机上的图表,我们都能通过产品数据与其他人沟通。It is the engineering product definition standard that ge
3、ometrically describes design intent and provides the documentation base for the design of the quality and production system.工程产品定义标准,几何尺寸描述设计意图,并为品质设计和产品系统提供文件基准。It is a technique of communication between Product Engineering and Manufacturing Engineering that promotes a uniform interpretation of the
4、 requirements for making a component.它是一种在产品工程和制造工程之间的技术交流,并促成一种针对零部件制造要求的唯一的解释。,GD&T for Body Engineering,5,What is GD&T什么是GD&T,GDT provides the dimensions of the component and the tolerances in a language that eliminates confusing and inconsistent notes,datum lines,and location point identificatio
5、ns,and replaces them with standard symbols that refer to a universal code.GDT提供部件的尺寸和公差,用一种语言,它能够消除混淆和不一致的注释,基准线,定位点辨认,并且用与一种通用的代码相关的标准符号替换他们。This code describes the dimensions and tolerances of the component with reference to the relationships of the features to each other and their functional inte
6、rfaces with mating parts,assemblies,etc.代码描述了关于部件间相互关系的特征的尺寸和公差,和他们匹配的部件的功能界面,总成等。,GD&T for Body Engineering,6,Authorisation批准,In 1990 Ford World-wide adopted the American National Standard for Dimensioning and Tolerancing,currently the ASME Y14.5M 1994.The authorisation for the above is documented
7、in Standard D-1 of the Ford Engineering CAD and Drafting Standards and is referenced on all our released data.在1990 福特全球范围内采用美国尺寸公差标准,目前的ASME Y14.5M 1994。This information can be accessed via Ford intranet;http:/above document also contains an electronic copy of the ASME Y14.5M 1994 Dimensioning and
8、Tolerancing Standard.,GD&T for Body Engineering,7,Application,The application of GDT is initially the responsibility of the relevant Component Engineer,however teamwork is the key to the correct application through the component Core Team.This provides the opportunity for all disciplines to contribu
9、te their part of the total design package.It ensures part data will satisfy design intent as well as manufacturing and inspection requirements based on function,machine capability and available technology.,GD&T for Body Engineering,8,Application,It provides the opportunity for proper Datum selection
10、 and has the potential to significantly reduce product changes,especially those changes following final product release.The Core Team should consist at a minimum of representatives from Product Engineering,Design Engineering,Manufacturing Engineering,and Quality Engineering.,GD&T for Body Engineerin
11、g,9,More information,Ford Engineering CAD and Drafting Standardshttp:/Applicationhttp:/,GD&T for Body Engineering,10,How GD&T Relates to Ford,The correct application has the potential to;Influence Fit and FinishReduce ReworksIncrease ReliabilityAffects Assembly ProcessReduce cost,GD&T for Body Engin
12、eering,11,The 5 Step Process,1,2,3,4,5,GD&T for Body Engineering,12,5 Step Process,1Utilise the new Design Concept2Establishment of the Datum Reference Frame3Establish GD&T Controls4Establish Tolerances5Final Approval of GD&T on Cad Data,GD&T for Body Engineering,13,Step 1,Utilise new design concept
13、,GD&T for Body Engineering,14,Utilise new design concept,The 1st step involves making decisions at the basic design stage that will ultimately effect the design,manufacture and verification of the final component.This can only be successfully achieved by the relevant PD representative attending the
14、Master Control Plan(MCP)Meetings.,GD&T for Body Engineering,15,Master Control Plan,What is the purpose of the MCP meeting in relation to PDTo establish a common understanding for the verification process of the major panels,e.g.Bodyside,Hood,Deck Lid,Door,Roof,Underbody,etc.To obtain agreement at an
15、 early stage of the design for the datum reference frame,die approach,etc.Who attends the MeetingPD and Manufacturing,i.e.Body Engineering,DCD,Stamping,Body and Assembly.,GD&T for Body Engineering,16,Master Control Plan,When should the Meeting take place.Initial design concept stage,knowing the comp
16、onents parameters such as size and function Current methods use;Past evidence,past experience,can sometimes hinder rather than assist the new design conceptResult of meetingMay be documented in CAD,or paper form,GD&T for Body Engineering,17,Step 2,Establish Datum Reference Frame,GD&T for Body Engine
17、ering,18,Establish Datum Reference Frame,As part of the Master Control Plan(MCP)Process meeting,Body Engineering and Manufacturing agreed to the definition of the Datum Features and their location.PD have Ownership of the Datum Features.,GD&T for Body Engineering,19,Datum Reference Frame(Reference P
18、ocket Guide,Page 8),Consists of a set of three mutually perpendicular planes,The reference frame exists in theory only and is not on the part,Sufficient datum features are used to position the part in relation to the Datum Reference Frame.,GD&T for Body Engineering,20,Datum Features,An actual featur
19、e of the part used to stage/position the part in the equipment for purposes of relating its geometry to the Datum Reference Frame.,GD&T for Body Engineering,21,Primary Datum Plane,Achieved by establishing a minimum of three Points to define a plane,GD&T for Body Engineering,22,Primary Datum Plane,Pr
20、imary Datum Plane should be Parallel to Die Plane,GD&T for Body Engineering,23,Primary Datum Plane,When Datum Target Areas defining Primary Datum Plane are not on one single planar surface,they must be controlled one to another using the PROFILE of a SURFACE geometric control.,GD&T for Body Engineer
21、ing,24,Supporting a panel only on the designated Datum Target Areas,effectively removes 3 degrees of freedom,i.e.1 Linear and 2 Rotational.,GD&T for Body Engineering,25,Datum Target Areas,Datum Target Areas should wherever possible be planar and parallel to the die plane.,Primary Datum Plane,GD&T fo
22、r Body Engineering,26,Datum Target Areas,Dedicated Datum Target Areas makes both the part,and gauge/fixture more robust,cost effective and Improves repeatability,GD&T for Body Engineering,27,Secondary Datum Feature,Generally a Datum Feature of Size is used,i.e.Single circular Hole,positioned on a su
23、rface that is parallel to the Primary datum Plane,and is ultimately used as a four way locator.,GD&T for Body Engineering,28,Secondary Datum Feature,Controlled relative to the Primary Datum Plane using the Geometric control PERPENDICULARITY.,GD&T for Body Engineering,29,Secondary Datum Feature,The i
24、ntersection of the derived axis of the feature perpendicular to the Primary Datum Plane,and the design side of the component is the local origin of all basic dimensions;0,0,0,GD&T for Body Engineering,30,Supporting a panel on the designated Datum Target Areas,and using the four way locator removes a
25、nother 2 Linear degrees of freedom,resulting in all 3 Linear,and 2 Rotational degrees of freedom constrained.,GD&T for Body Engineering,31,Tertiary Datum Feature,Generally the width of a Slotted Feature of Size is used as a two way locator.,GD&T for Body Engineering,32,Tertiary Datum Feature,To elim

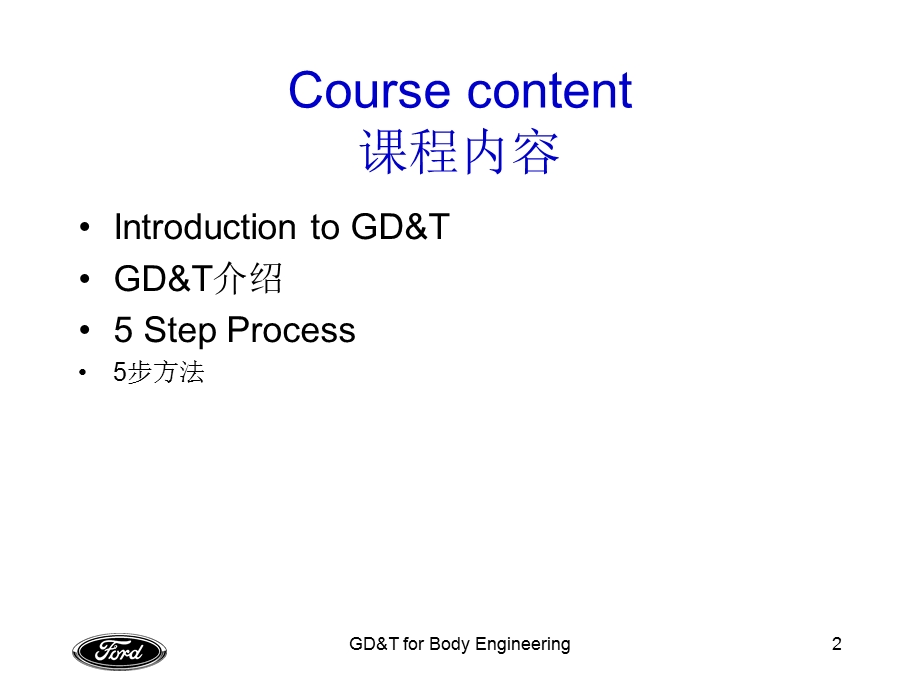
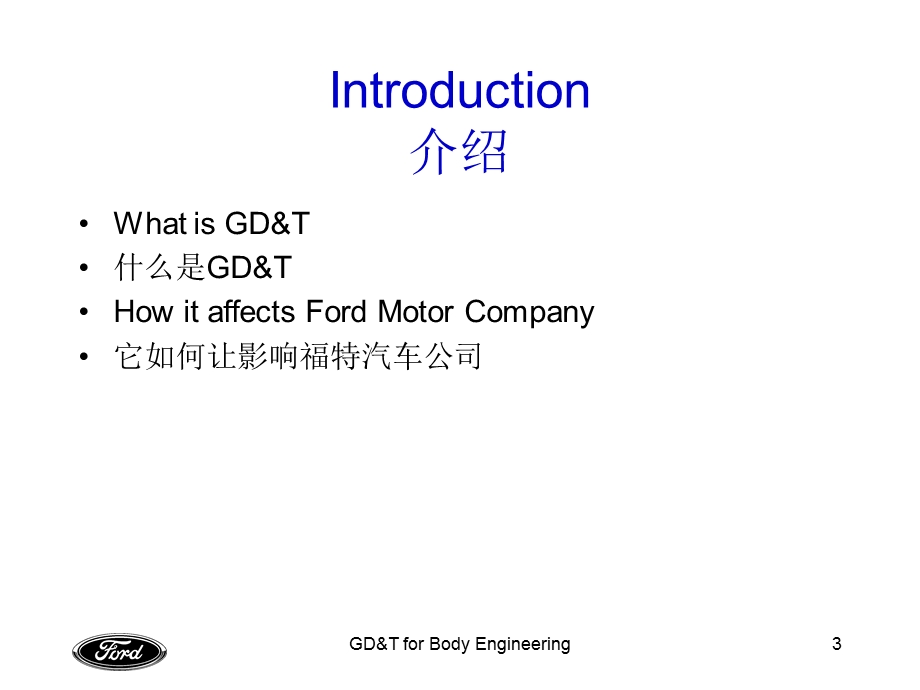
- 配套讲稿:
如PPT文件的首页显示word图标,表示该PPT已包含配套word讲稿。双击word图标可打开word文档。
- 特殊限制:
部分文档作品中含有的国旗、国徽等图片,仅作为作品整体效果示例展示,禁止商用。设计者仅对作品中独创性部分享有著作权。
- 关 键 词:
- Ford 福特 GDT 公差 培训 材料 全集

链接地址:https://www.31ppt.com/p-2901614.html