数控加工技术ppt课件.ppt
《数控加工技术ppt课件.ppt》由会员分享,可在线阅读,更多相关《数控加工技术ppt课件.ppt(532页珍藏版)》请在三一办公上搜索。
1、第1章 绪论,第2章 金属切削基础,第3章 数控加工工艺的设计,第4章 数控车削工艺知识,第5章 数控镗铣削加工工艺知识,第6章 数控编程基础,第7章 数控车削加工编程,第8章 数控镗铣削加工编程,第1章绪 论,1.1 数控加工的基本知识,1.2 数控机床的分类,1.3 数控机床的工作原理及组成,1.4 数控机床的主要性能指标,第1章绪 论,1.1数控加工的基本知识,1.1.1数控加工的基本概念,数控机床,是指采用数字程序进行控制的机床。,1.1.2 数控机床的产生,数字控制机床就是为了解决单件、小批量、特别是复杂型面零件加工的自动化并保证质量要求而产生的。 机床数控系统的发展经历了两个阶段共
2、六代。 1.数控(NC)阶段 2.计算机数控(CNC)阶段,我国的数控技术发展过程可划分为四个阶段:第一阶段: 1958-1965年,处于试制、试用阶段。第二阶段: 从1965年开始,已开始从试验阶段进入生 产试用阶段。第三阶段: 1972-1979年,是数控技术的生产和试用 阶段。第四阶段: 1980年以后,是稳定发展阶段。,1 高速化 2 高精度化 3 复合化 4 控制智能化 5 互联网络化 6 计算机集成制造系统,第1章绪 论,1.1.3 数控技术的发展方向,车铣复合中心加工复杂零件,数控机床由主传动、进给传动机构,滚珠丝杠螺母副、导轨副、自动换刀装置及回转工作台机械结构构成。 1数控机
3、床的支承件 2数控机床的主传动系统 3数控机床的进给系统 4数控机床导轨 5其他装置,第1章绪 论,1.1.4 数控机床的机械结构,1.2 数控机床的分类,1.普通数控机床 2.数控加工中心 3.特种加工机床类 4.板材加工类数控机床,第1章绪 论,1.2.1 按加工工艺方法分类,专用数控机床加工阀类零件,1.2.2 按运动方式分类,(2)直线控制系统(Straight-line Control),(1)点位控制系统(Positioning Control),第1章绪 论,(3)轮廓控制系统(Contour Control) 运动轨迹是任意斜率的直线、圆弧、螺旋线等。,第1章绪 论,1.2.2
4、 按运动方式分类,1.开环控制数控机床,1.2.3按伺服系统的控制方式分类,第1章绪 论,2.闭环控制数控机床,3.半闭环控制数控机床,图1-7,第1章绪 论,1.2.2 按运动方式分类,1.二轴联动 同时控制两轴运动,1.2.4按联动坐标轴的个数分类,2.两轴半联动 其中两轴联动,另一轴作周期运动,3. 三轴联动 (1)X、Y、Z三个坐标轴联动(2)除了同时控制X、Y、Z其中两个坐标 轴联动外,还同时控制围绕其中某一坐标轴旋转的旋转坐标轴。,第1章绪 论,4. 四轴联动,5. 五轴联动,1.2.4按联动坐标轴的个数分类,五轴联动,1.3数控机床的工作原理及组成,1.3.1数控机床的组成,第1
5、章绪 论,1.3.2 数控机床的基本工作原理,图1-13 数控机床的加工过程1-CNC control CNC控制 2-Technological processing 技术处理 3-Geometrical processing 几何处理 4-Adjustment control 调节 5-Axis control 控制各轴 6-Actual Position value 实际位置值,第1章绪 论,1. 定位精度和重复定位精度 定位精度是指实际位置与数控指令位置的一致程度。不一致量表现为误差。 2. 分度精度 分度精度是指分度工作台在分度时,指令要求回转的角度值和实际回转的角度值的差值。,1.
6、4 数控机床的主要性能指标,1.4.1 数控机床的精度,1.4.2 数控机床的控制轴数与联动轴数,第1章绪 论,数控机床的运动性能指标主要包括主轴转速、进给速度、坐标行程、回转轴的转角范围、刀库容量及换刀时间等。 1. 最高主轴转速和最大加速度 2. 最高快移速度和最高进给速度 3. 行程 4. 回转轴的转角范围 5. 刀库容量和换刀时间,1.4.3 数控机床的运动性能指标,第1章绪 论,第一章 结束,第2章 金属切削基础,2.1 切削运动和切削用量的概念,2.2 金属切削刀具,2.3 金属切削过程基本规律,2.4 刀具几何参数的合理选择,2.5切削用量及切削液的选择,金属切削过程就是用金属切
7、削刀具把工件毛坯上预留的金属材料切除,达到零件精度要求的过程。切削中,刀具和工件之间必须有相对运动,这种相对运动就称为切削运动。按切削运动在切削加工中所起的作用不同,可分为主运动和进给运动。,2.1 切削运动和切削用量的概念,2.1.1 切削运动,1. 主运动刀具与工件之间产生相对运动,直接切除工件上的切削层,使之转变为切屑,从而形成工件新表面的基本运动。主运动是由机床提供的主要运动。如图2-1所示,,图2-1切削运动和工件表面,注:从主运动的形式上看,它分为直线运动和回转运动两大类。,2. 进给运动进给运动是不断的把切削层投入到切削中去的运动。 3. 加工中形成的工件表面切削过程中,工件上多
8、余的材料不断地被刀具切除而转变为切屑,因此,工件在切削过程中形成了三个不断变化的表面(见图2-2),即已加工表面、加工表面和待加工表面。,图2-2加工中形成的表面a)车外圆 b)车内孔 c)车端面,2.1 切削运动和切削用量的概念,1. 背吃刀量(p)背吃刀量是已加工表面和待加工表面之间的垂直距离,其单位为米。,2.1.2 切削用量的概念,2. 进给量(f),3切削速度(vc)切削刃选定点相对于工件主运动的瞬时速度称为切削速度。,d切削刃选定点处所对应的工件或刀具的回转直径(mm);工件或刀具的转速(r/min)。,n工件或刀具的转速(rmin),图2-3,1. 切削厚度hD 2. 切削宽度b
9、D 3. 切削面积AD,2.1.3切削层参数,图2-4 车外圆时切削层的参数,1.切削部分的组成包括: (1) 前刀面:刀具上切屑流过的表面。一般来讲是指刃磨后的断屑槽表面。 (2) 主后刀面 (3) 副后刀面 (4) 主切削刃 (5) 副切削刃 (6) 刀尖,2.2 金属切削刀具,2.2.1刀具切削部分组成要素,图2-8 刀具的几何形状,1.确定刀具角度的平面正交参考系刀具几何参数的确定需要以一定的参考坐标系和参考坐标平面为基准。,2.2.2 刀具切削部分的几何角度,图2-9 平面正交参考系,(1)基面(Pr):通过切削刃的某一选定 点,垂直于该点切削速度方向的平面。(2)切削平面(Ps):
10、通过切削刃选定点,垂直于基面的平面。(3)正交平面(Po):通过主切削刃选定点,分别与基面和切削平面垂直的平面。,2. 刀具的标注角度 (1)在正交平面中测量的角度 1)前角0 2)后角0 3)偰角 (2)在基面中测量的角度 1)主偏角kr 2)副偏角kr 3)刀尖角r,r,2.2.1刀具切削部分组成要素,(3)在切削平面中测量的角度 刃倾角s,(4)在副正交平面内测量的角度 副后角0,图2-10 刀具的几何角度,2.2.1刀具切削部分组成要素,2. 刀具的标注角度,2.2.1刀具切削部分组成要素,2. 刀具的标注角度,前角后角主偏角r副偏角r副后角o刃倾角S,车刀六个角度,2.2.1刀具切削
11、部分组成要素,2. 刀具的标注角度,刀具材料主要是指刀具切削部分的材料 1刀具材料应具备的性能 (1)高的硬度和耐磨性 (2)足够的强度和韧性 (3) 良好的耐热性和导热性 (4)良好的工艺性 (5)经济性,2.2.3 刀具材料,2.2 金属切削刀具,2. 刀具材料的种类(1)高速钢 高速钢是含有较多的钨、铬、铝、钒等合金元素的高合金工具钢。 1)通用型高速钢:常用牌号有W18Cr4V和W6Mo5Cr4V2。 2)高性能高速钢:高性能高速钢是在通用型高速钢的基础上,通过增加碳、钒的含量或添加钴、铝等合金元素而得到的耐热性、耐磨性更高的新钢种。常用牌号有:90W18Cr4V、9W6Mo5Cr4V
12、3、W6Mo5Cr4V2Co8、及W6Mo5Cr4V2Al等。,2.2 金属切削刀具,(2)硬质合金 硬质合金是硬度和熔点都很高的碳化物(如WC、TiC、NbC等),用Co、Mo、Ni作粘合剂高温高压制成的粉末冶金制品。 1)钨钴类硬质合金(YG):以碳化钨做硬质相、钴为粘结相高温、高压粉末冶金得到的硬质合金。常用的牌号有:YG8、YG6、YG3,数值代表钴的含量。分别适用于粗加工、半精加工和精加工。ISO标准中又称K类。 2)钨钛钴类硬质合金(YT):以碳化钨、碳化钛做硬质相,钴为粘结相粉末冶金得到的硬质合金。常用的牌号有YT5、YT15、YT30等,其中的数字表示碳化钛的含量。ISO标准中
13、又称P类。 3)钨钛钽(铌)类硬质合金(YW):在钨钛钴类硬质合金中加入少量的碳化钽(TaC)或碳化铌(NbC),所形成一种硬质合金。是一种综合性能较好的刀具材料。常用牌号有YW1和YW2,ISO标准中又称M类。,2.2 金属切削刀具,2. 刀具材料的种类,2.2 金属切削刀具,2. 刀具材料的种类,(3)其他刀具材料 1) 涂层刀具材料:这种材料是在韧性较好的硬质合金 体上或高速钢基体上,采用化学气相沉淀(CDV)法或物理气相沉淀(PVD)法涂覆一薄层硬度和耐磨性极高的难熔金属化学物而得到的刀具材料。 2) 陶瓷刀具材料:其主要成分是Al2O3 3)金刚石刀具材料:金刚石分为人造和天然两种。
14、 4)立方氮化硼(CBN):人工合成的一种高硬度材料,其硬度可达73009000HV,可耐13001500的高温,与铁族元素亲和力小。,2.2 金属切削刀具,2. 刀具材料的种类,1切屑的形成过程 金属的切削过程是将工件上多余的金属层通过切削加工被刀具切除而形成切屑的过程。把切削区域划分为三个变形区:第变形区(剪切滑移区);第变形区(滞流层);第变形区( 加工硬化、残余应力 ),2.3 金属切削过程基本规律,图2-11三个形变区的划分,2.3.1切屑的形成及种类,2.3 金属切削过程基本规律,2.3.1切屑的形成及种类,2. 切屑的种类,(1)带状切屑 (2)挤裂切屑 (3)单元切屑(4)崩碎
15、切屑,图2-13切屑的种类a)带状切削 b) 节状 c) 单元状 d) 崩碎状,2.3 金属切削过程基本规律,2.3.1切屑的形成及种类,2.3 金属切削过程基本规律,2.3.2 切削力与切削热,1. 切削力的来源及分解,3个变形区产生的弹、塑性变形抗力切屑、工件与刀具间摩擦力。,切削力分解,切削力来源,2.3 金属切削过程基本规律,2.3.2 切削力与切削热,2. 影响切削力的主要因素(1)工件材料的影响 (2)切削用量的影响,切削深度与切削力近似成正比; 进给量增加,切削力增加,但不成正比; 切削速度对切削力影响复杂如图,刀具几何角度影响前角0 增大,切削力减小主偏角r 对主切削力影响不大
16、,对吃刀抗力和进给抗力影响显著( r Fp,Ff,),2.3 金属切削过程基本规律,2.3.2 切削力与切削热,2. 影响切削力的主要因素,刃倾角s对主切削力影响不大,对吃刀抗力和进给抗力影响显著( s Fp,Ff) 刀尖圆弧半径 r 对主切削力影响不大,对吃刀抗力和进给抗力影响显著( r Fp,Ff) 刀具材料:与工件材料之间的亲和性影响其间的摩 擦,而影响切削力 ; 切削液:有润滑作用,使切削力降低 ;后刀面磨损:使切削力增大,对吃刀抗力Fp的影响最为显著。,2.3 金属切削过程基本规律,2.3.2 切削力与切削热,2. 影响切削力的主要因素,切削过程变形和摩擦所消耗功,绝大部分转变为切削
17、热 主要来源 QA=QD+QFF+QFR QD , QFF , QFR分别为切削层变形、前刀面摩擦、后刀 面摩擦产生的热量 切削热传出 切削热由切屑、工件、刀具 和周围介质(切削液、空气)等 传散出去。,2.3 金属切削过程基本规律,2.3.2 切削力与切削热,3. 切削热与切削温度,2.3 金属切削过程基本规律,2.3.2 切削力与切削热,3. 切削热与切削温度,1)切削用量对切削温度的影响 切削速度对切削温度的影响最大,v切削温度而背吃刀量对切削温度的影响很小。,2)刀具几何参数的影响 前角o切削温度主偏角r切削温度负倒棱及刀尖圆弧半径对切削温度影响很小 0,3)工件材料的影响工件材料机械
18、性能切削温度工件材料导热性 切削温度,4)刀具磨损对切削温度的影响5)切削液对切削温度的影响,2.3 金属切削过程基本规律,2.3.2 切削力与切削热,3. 切削热与切削温度,1. 积屑瘤 在中速切削塑性较大的工件材料时,常在切屑刃口附近粘结一硬度很高(通常为工件材料硬度的23.5倍)的楔状金属块,它包围着切削刃且覆盖部分前刀面,这种楔状金属块称为积屑瘤,也称刀瘤。如图2-15所示。,2.3.3、切削加工中的物理现象,图2-15 积屑瘤及其对切削的影响,2.3 金属切削过程基本规律,(1)积屑瘤的形成(2)积屑瘤形成的条件 当压力达到2000N/mm23000N/mm2以上,切削温度约300左
19、 右时(3)积屑瘤在切削过程中的作用。 1)保护刀具 2)增大实际前角 有积屑瘤的车刀,实际前角可增大至3035,因 而减少了 切屑的变形,降低了切削力。 3)影响工件表面质量和尺寸精度,2.3.3、切削加工中的物理现象,2.3 金属切削过程基本规律,(4)影响积屑瘤的主要因素及防止方法 1)切削速度 2)进给量的影响 3)刀具角度的影响 4)切削液的影响,图2-16 切削速度对积屑瘤的影响,2. 加工硬化 (1)加工硬化的形成 (2)加工硬化对切削加工的影响 加工硬化会使下道工序的切削难以进行,刀具磨损加 快;切削时应尽量保持车刀刃口锋利。,图2-17 加工硬化的形成,1、前角的选择 (1)
20、前角的作用:前角的功用主要调整刀具的锋利程度。 (2)合理前角的选择原则 1)根据工件材料选取前角。 2)根据刀具材料选取前角。 3)根据加工阶段选择选取前角。 4)根据工艺系统刚性和机床功率选取前角。,2.4 刀具几何参数的合理选择,2.4.1 刀具几何角度的选择及选择原则,2.后角的选择 1)后角的功用 减小主后刀面与过渡表面的弹性恢复层之间的摩擦, 减轻刀具磨损。 2)合理后角的选择原则 粗加工:o , 精加工:o 塑性材料:o , 脆性材料:o; 硬度高:o , 强度高o 工艺系统:刚度高o,2.4 刀具几何参数的合理选择,2.4.1 刀具几何角度的选择及选择原则,3. 主偏角及副偏角
21、的选择 (1)主偏角的功用:主要影响刀具耐用度、已加工表面粗糙度及切削力的大小。 (2)主偏角的选择原则 1)根据加工阶段选择 2)考虑工件材料的硬度 3)考虑工艺系统刚性 4)根据工件的轮廓选择 (3)副偏角的功用:主要是减小副切削刃和已加工表面的摩擦。 (4)副偏角的选择原则 1)一般刀具的副偏角 ,在不引起振动的情况下,可选取较小的副偏角,如车 刀、刨刀均可取r=5度10度. 2)精加工刀具的副偏角应取的小一些,减小表面粗糙度。 3)加工强度、高硬度材料或断续切削时,取较小的副偏角(r =4度6度) 4)切断刀、锯片刀和槽铣刀,只能取很小的副偏角。(r =1度2度),2.4 刀具几何参数
22、的合理选择,2.4.1 刀具几何角度的选择及选择原则,2.4 刀具几何参数的合理选择,2.4.1 刀具几何角度的选择及选择原则,4.刃倾角s的选择 (1)刃倾角的功用:主要影响切削流向和刀尖强度。 (2)刃倾角的选择原则 1)粗加工S 0(使FP 小些) 2)断续切削:S 0(使FP小些) 5)微量切削:S取大值(使刀具实际刃口半径),2.4 刀具几何参数的合理选择,2.4.1 刀具几何角度的选择及选择原则,1.刀具磨损形式 刀具失效的形式分为正常磨损和破损两大类,2.4.2刀具磨损与刀具寿命,图2-20 正常磨损的几种形式a)后刀面磨损 b)前刀面磨损 c)前后刀面磨损,2.刀具磨损过程与磨
23、钝标准 (1)刀具磨损过程:在一定切削条件下,不论何种磨损状态,其磨损量都将随切削时间的增长而加大(见图2-22)。由图可知。刀具磨损过程可分为三个阶段。,图2-22刀具磨损的过程,(2)刀具的磨钝标准;刀具磨损到一定程度后,切削力、切削温度显著增加,加工表面变得粗糙,工件尺寸可能会超出公差范围,切屑颜色、形状发生明显变化,甚至产生振动或出现不正常的噪声等,这些现象都可说明刀具已经磨钝。,2.4.2刀具磨损与刀具寿命,3.刀具寿命 (1)刀具寿命:指的是从刀具刃磨后开始切削,一直到磨损量达到 磨钝标准为止所经过的总切削时间,用字符T表示,单位min。 (2)影响刀具耐用度的因素: 1)切削用量
24、的影响。切削用量是影响刀具耐用度的一个重要因素。 2)刀具几何参数。 3)刀具材料到的影响。 4)工件材料的影响。,2.4.2刀具磨损与刀具寿命,第3章 数控加工工艺的设计,3.1 工件定位原理及基准的选择,3.2 常用的定位方法及定位误差分析,3.3 数控机床夹具,3. 4 数控加工工艺规程设计,3.1工件定位原理及基准的选择,3.1.1 工件定位原理,1.六点定位原理,图3-1 工件在空间的六个自由度,如图3-1所示, 一个工件在三维空间具有六个自由度,因此,要完全确定工件的位置,就必须消除这六个自由度,通常用六个支承点(即定位元件)来消除工件的六个自由度,其中每一个支承点限制相应的一个自
25、由度,这就是工件的“六点定位原理”。,X 、 Y 、 Z、X、Y、Z,水平面 X、 Y、Z,左侧面 X Z,后侧面 Y,(1) 完全定位(2) 不完全定位(3) 欠定位,图3-3 限制自由度与加工要求的关系,(4)过定位,a) b) 图3-4 过定位实例a) 长销和大端面定位 b) 平面和两短圆柱定位,2. 定位与夹紧的关系,1)夹紧: 工件在夹具中定位后必须夹紧才能进行 加工。夹紧是靠夹紧装置来完成的。 2)定位与夹紧的关系: 对于定位而言,定位时,必须使工件的定位基准紧帖在夹具的定位元件上,否则不称其为定位,而夹紧的作用则是使工件不离开定位元件。,1基准的概念 基准:就是零件上用来确定其他
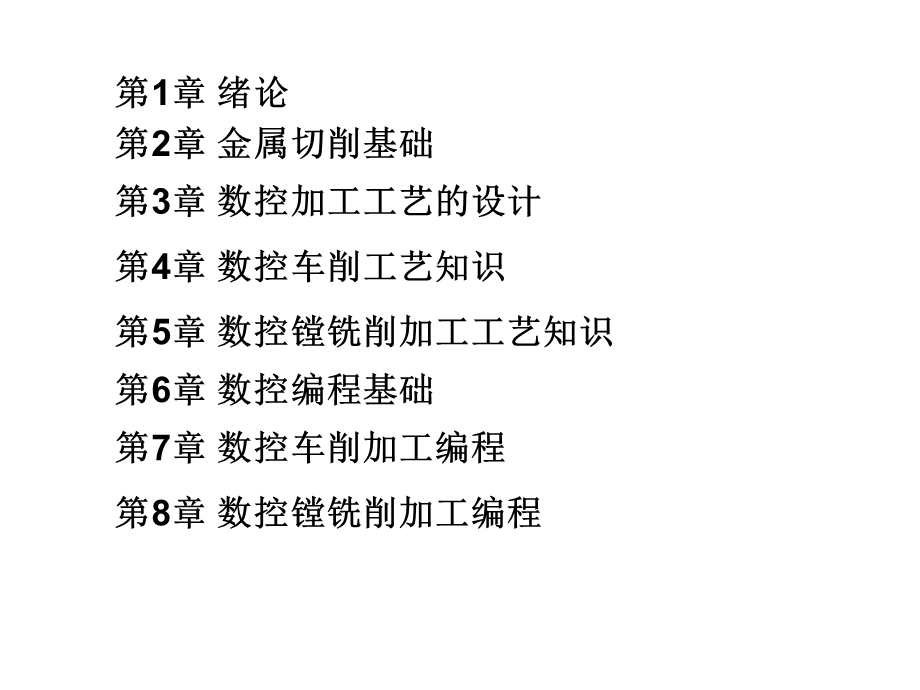

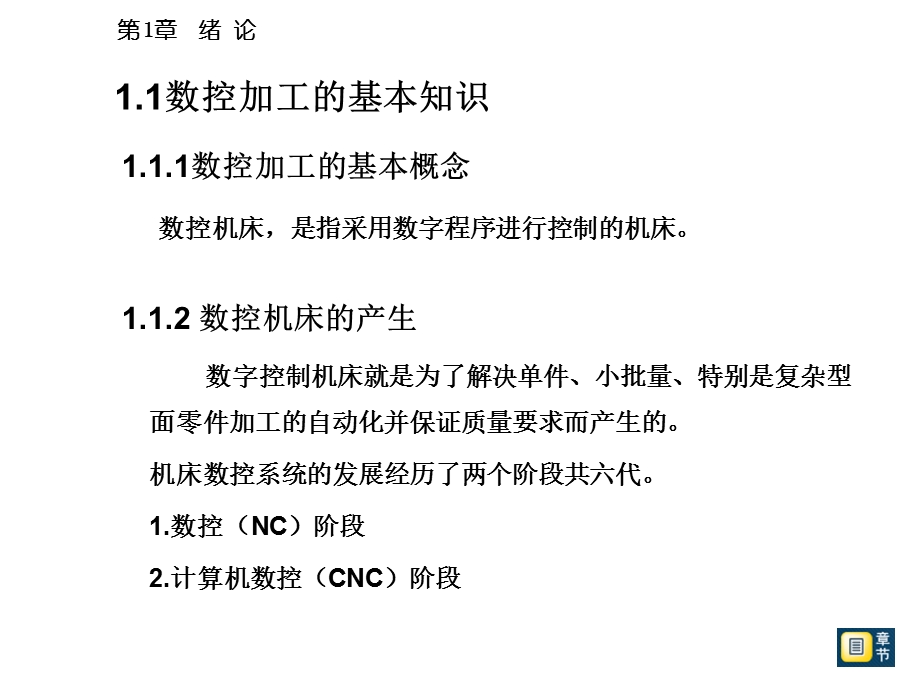
- 配套讲稿:
如PPT文件的首页显示word图标,表示该PPT已包含配套word讲稿。双击word图标可打开word文档。
- 特殊限制:
部分文档作品中含有的国旗、国徽等图片,仅作为作品整体效果示例展示,禁止商用。设计者仅对作品中独创性部分享有著作权。
- 关 键 词:
- 数控 加工 技术 ppt 课件

链接地址:https://www.31ppt.com/p-1470108.html